L'IoT en pince pour l'impression 3D
Pour lancer son produit IoT dédié à la maintenance prédictive des ascenseurs, la start-up parisienne WeMaintain a choisi de recourir à l'impression 3D. Tout comme la start-up rochelaise de thérapies digitales Ullo pour sa fleur connectée de relaxation. "La diversité des projets IoT et des acteurs sur le marché tire la demande pour la réalisation de prototypes en impression 3D", constate Clément Moreau, CEO de Sculpteo. Lancée en 2009 pour des réalisations destinées au grand public, l'entreprise française spécialisée dans l'impression 3D s'est orientée en 2013 vers le marché BtoB et, aujourd'hui, l'IoT représente 20% de son chiffre d'affaires.
Dans le secteur de l'IoT, les entreprises utilisent généralement cette technologie pour imprimer des boîtiers, des supports, des systèmes de fixation ou encore des connecteurs. "La demande concerne surtout des parties mécaniques", précise Clément Moreau. Trois méthodes sont utilisées pour l'impression 3D de ces pièces : l'impression par frittage de plastique, utilisée majoritairement pour les grands volumes, l'impression par stéréolithographie (SLA) sur résine, privilégiée pour les objets fragiles ou techniques, et l'impression par projection de matière. C'est cette dernière technique qu'a choisie WeMaintain. La start-up a souhaité prendre en main l'impression par elle-même, tandis que d'autres font appel à des spécialistes comme Nove3D ou Sculpteo, en particulier pour passer à l'étape de l'industrialisation.
Pour WeMaintain, le principal intérêt de l'impression 3D est de rendre possible très rapidement les itérations sur de petites séries de produits. "Notre capteur laser nécessitait d'être droit par rapport à la gaine. Pour cela, il fallait du sur-mesure en fonction des diverses portes d'ascenseur, explique Tristan Foureur, cofondateur et CTO de WeMaintain. Avec l'impression 3D, nous pouvons avoir un premier prototype en une demi-journée et le tester l'après-midi même sur le terrain." Au total, une cinquantaine de boîtiers différents ont été conçus avec leurs attaches, avant d'aboutir au produit final.
Des boitiers en impression 3D à moins de quatre euros
Les cofondateurs de WeMaintain apprécient être indépendants des fabricants et pouvoir effectuer des modifications comme ils l'entendent dans "une démarche de R&D permanente". "J'ai voulu ajouter une deuxième antenne 4G pour améliorer la réception du signal. Il m'a suffi d'une manipulation d'une heure et demi pour finaliser le complément", raconte Damien Weber, ingénieur IoT chez WeMaintain.
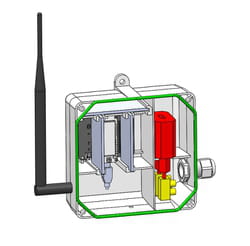
"L'impression 3D est idéale quand une entreprise part de zéro et veut s'assurer du fonctionnement de son produit", souligne Vincent Raquin, fondateur de Nove3D, bureau d'étude sur l'impression 3D à la Rochelle. Nove3D a réalisé 20 boîtiers pour la société de développement d'applications mobiles et d'objets connectés Ubidreams, qui voulait des capteurs pour suivre la position de camions sur un site de déchargement. Le concept validé, Ubidreams s'est doté de 50 devices. Avec l'impression 3D, les entreprises peuvent imprimer le nombre de pièces requises. "Un atout pour les grands groupes, ce qui leur évite le stockage de pièces. Ces dernières sont par ailleurs réalisées en France, en local, permettant une maîtrise de la fabrication", ajoute Vincent Raquin.
Le deuxième grand avantage de l'impression 3D mis en avant est son coût. "Une bobine de plastique d'un kilo revient à 20 euros environ. Un boîtier comprenant 80 grammes de plastique, son coût de production ne dépasse guère quatre euros", indique Damien Weber. La machine à impression 3D a coûté près de 700 euros à WeMaintain, quand la réalisation de moules pour les volumes nécessaires serait revenue à un prix compris entre 20 000 et 40 000 euros. "La baisse des coûts de l'impression 3D reste un enjeu important", affirme Clément Moreau, chez Sculpteo.
Le temps d'impression et la gestion des produits imprimés restent les deux challenges auxquels font face les utilisateurs. "Nous avons réduit le plastique, la taille du boîtier et le placement des composants à l'intérieur pour passer de 14 à 4 heures d'impression, et j'ai réalisé un extracteur de produits pour pouvoir imprimer en continu sans intervention humaine à la fin de chaque impression", détaille Damien Weber. WeMaintain peut ainsi fabriquer une centaine de boîtiers par semaine, ce qui lui permet de s'adapter à la demande des clients. En 3D et en temps réel donc.