Avec le projet 5G Steel, ArcelorMittal connecte l'une des plus grandes usines d'Europe
L'usine sidérurgique de Dunkerque du groupe ArcelorMittal, avec ses 450 hectares, est l'une des plus importantes d'Europe occidentale. Au cœur de son activité de laminage à chaud : le train continu à chaud. C'est dans un immense hangar de 600 mètres de long, où s'élèvent des volutes de vapeur dans un bruit assourdissant, que des plaques d'acier évoluent à une vitesse de 50 à 70 km/h pour être refroidies et transformées en bobines d'acier sur ce train continu à chaud. Ce laminoir n'a jamais bénéficié de connectivité. "Installer des câbles de fibre optique ou des routeurs wifi sur ses 600 mètres de long aurait engendré des coûts trop importants", explique David Glijer, directeur de la transformation digitale d'ArcelorMittal France. Avec le projet 5G Steel, dont l'objectif est de déployer un réseau 5G privé industriel sur le site, cette connexion est devenue possible.
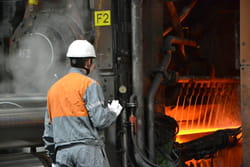
Tout au long du train continu à chaud, le projet 5G Steel a ancré le digital dans les processus et favorisé l'apparition d'opérateurs connectés, pour l'instant grâce à la 4G LTE. Les usages sont divers : les opérations de relevé, de maintenance, d'audit ou de consignation se font sur le terrain sur tablette. Les opérateurs n'ont plus besoin de retourner au bureau pour transmettre les informations à insérer dans le logiciel, avant d'effectuer une opération. Tous les opérateurs portent un casque – obligatoire – qui a vocation à être connecté pour transmettre des images au cockpit de commande, que ce soit celui du train continu, au milieu du lieu, ou au cockpit du Digital Lab d'ArcelorMittal, situé à quelques kilomètres près du port de Dunkerque. ArcelorMittal a organisé ce jeudi 2 février une visite presse, à laquelle a participé le JDN, pour montrer que le plus grand réseau 4G/5G en environnement industriel est désormais opérationnel.
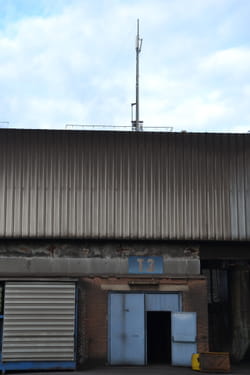
Le projet, annoncé le 23 novembre 2021, a été mis en place "dans des temps records", se félicite Franck Bouétard, PDG d'Ericsson France qui a fourni l'équipement. Après la définition du positionnement des antennes, validé le 8 décembre 2021, Ericsson a approvisionné le matériel trois mois plus tard, le 8 février 2022, et a installé le cœur en redondance et la première antenne le 22 avril 2022. L'installation a été finalisée le 5 août 2022, ce sont désormais 9 sites radios et 19 routeurs qui couvrent 10 km². L'obtention de l'utilisation des fréquences par l'Arcep le 1er septembre 2022 a conduit à l'allumage du réseau sur le site le 13 octobre 2022. Les opérateurs opèrent eux-mêmes le réseau depuis cette date. "Nous n'en sommes plus à la simple expérimentation", soutient David Glijer, qui ne veut pas communiquer le coût du projet mais affirme que déployer du wifi pour ces usages aurait multiplié le budget par quatre.
La 5G au service de la décarbonation
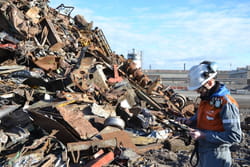
En parallèle au train continu à chaud, un deuxième usage de 5G Steel domine sur le site de Dunkerque, à savoir l'inspection mobile de la qualité de l'acier recyclé. ArcelorMittal en fait un axe fort dans son objectif de décarbonation : réduire de 35% ses émissions en 2030 avant d'atteindre la neutralité carbone. Concrètement, là encore les opérateurs sont équipés de tablettes pour faire à l'extérieur, sur un vaste terrain où sont déposés les morceaux d'acier arrivés par camion, leur rapport sur la densité et la composition de l'acier. 14 routeurs 4G/5G durcis pour véhicules ont été déployés.
Le projet n'en est qu'à ses débuts, le réseau utilisé étant de la 4G LTE. ArcelorMittal est encore loin de bénéficier de la 5G, et plus encore du network slicing, pour lequel le groupe est toujours en discussion avec l'Arcep. Mais le groupe se réjouit déjà des résultats : "Nous avons observé des gains sur la latence, qui n'est que de 20 millisecondes, et les solutions offrent une réelle satisfaction à nos opérateurs, qui gagnent en rapidité d'exécution en évitant des trajets inutiles, ainsi qu'en sécurité et en confort", raconte David Glijer, qui avait pourtant un doute au départ en raison de l'environnement métallique et du nombre de points hauts. "Nous avons réussi à faire fonctionner la connectivité dans cet environnement par un bon design, indique Valérie Cussac, vice-présidente exécutive Smart Mobility Services chez OBS, intégrateur du projet. Il s'agit de déterminer précisément où placer les antennes – ni trop espacées pour que le réseau reste performant, ni trop rapprochées pour éviter de faire exploser les coûts. Ce projet est la base des fondations avant une transformation réelle."
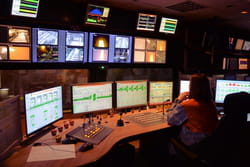
Les perspectives sont encore nombreuses, le groupe a d'autres usages en réflexion. ArcelorMittal collabore avec la start-up belge Otiv dans la mise en place de véhicules ferroviaires autonomes à Dunkerque et à Florange. "Quand la 5G sera progressivement déployée, elle sera cruciale pour cet usage qui réclame du temps réel", rappelle Franck Bouétard, qui anticipe également le déploiement de robots pilotés depuis les cockpits de commandes. De son côté, OBS va mener des tests dans les semaines à venir sur l'hybridation des réseaux, pour permettre aux opérateurs de basculer du réseau privé au réseau public en fonction des besoins.
L'IoT sera également un chantier de taille. Le réseau 5G déployé permettra de connecter 50 000 objets connectés. Aujourd'hui, seul 1 000 le sont, dont les 160 tablettes pour la maintenance des équipements et les 130 tablettes des managers postés qui supervisent les opérateurs. Les attentes sont fortes : "Une ligne de production compte près de 200 capteurs. Sachant qu'il y a 65 lignes, nous pourrions faire remonter les informations de plus de 13 000 capteurs", confie David Glijer. La difficulté, reconnaît Valérie Cussac, est le manque actuel de capteurs compatibles avec la 5G : "Pour que les déploiements se concrétisent, il faut une plus grande variété de capteurs certifiés dédiés aux environnements critiques. Cet écosystème n'est pas encore développé."
Enfin, les projets menés sur ce site pilote, qui produit 200 000 tonnes d'acier par jour, seront répliqués sur les autres sites d'ArcelorMittal (les travaux en ce sens ont démarré à Florange) et seront au cœur du site de Mardyck (Hauts-de-France), dont la nouvelle activité de production d'acier électrique sera nativement digitalisée. Pour cette production dédiée aux véhicules électriques, la 5G et l'intelligence artificielle seront au cœur des processus. ArcelorMittal veut prouver que dans son métier, la 5G et l'innovation vont bon train.